Maintenance Management From 0 To Hero
Eric Dao
2:06:55
Description
Maintenance methodology training for a professional maintenance management
What You'll Learn?
- Understand maintenance fundamentals, foundations
- Understand maintenance management methodology from 0 to advanced
- Define step by step to build a high-effective maintenance system
- Define step by step to reduce machine downtime over 50% and improve MTBF (Mean Time Between Failures) by over 50% in 6 months
- Define step by step to increase OEE (Overall Equipment Efficiency) by at least 7% in 6 months
- Define step by step to reduce maintenance costs by approximately 10% annually.
- Improved peace of mind allows for restful nights and days off.
Who is this for?
What You Need to Know?
More details
DescriptionHello everyone, I'm Eric Dao, I bring several years of experience in maintenance engineering, fortunate to work in environments with excellent maintenance foundations. This has allowed me to accumulate a robust maintenance foundations, of which I am extremely proud and have full confidence in.
The maintenance foundations includes fundamental maintenance principles, it is core methodology. Anyone aiming for success in maintenance must thoroughly understand and adhere to these principles.
This training encapsulates the essence of the maintenance foundations that I've learned, applied, and compared across various companies. To me, it is invaluable, and I wish to share these insights with those fortunate enough to encounter them.
I confirm that this is the most practical and realistic lecture on maintenance foundation across all platforms.
Reflecting on my experience, I have not change many companies. I have spent time to fully experience the maintenance systems of each manufacturing plant. I have worked for an international food and beverage company and later for an electronic equipment manufacturing company. I believe my maintenance foundations are universally applicable and definitely brings substantial and tangible benefits.
To prove my claims, here are some key performance indicators (KPIs) that improved after implementing the maintenance foundations:
1. Machine downtime significantly reduced by over 25% in the first 3 months, followed by a 50% reduction in 6 months. Mean Time Between Failures (MTBF) increased by over 50% from 24.5 hours to 51 hours. Note: These figures may vary depending on the industry and machine conditions.
2. Overall Equipment Efficiency (OEE), a measure of machine performance, increased by at least 7%, reaching approximately 90% after 6 months.
3. Maintenance costs reduced by approximately 10% annually.
Lastly, and importantly for us maintenance engineers, improved peace of mind allows for restful nights and days off.
With my experience and maintenance principles in mind, if existing maintenance foundations are not implemented effectively, advanced maintenance methods such as Total Productive Maintenance (TPM) or Reliability-Centered Maintenance (RCM) should not be applied.
Enroll and increase your maintenance/machine performance now!
Who this course is for:
- All engineers need to improve maintenance/machine performance
- Engineers who implemented TPM/RCM but not successfully
- Fresh maintenance engineers
- Engineering students want to learn about maintenance management
Hello everyone, I'm Eric Dao, I bring several years of experience in maintenance engineering, fortunate to work in environments with excellent maintenance foundations. This has allowed me to accumulate a robust maintenance foundations, of which I am extremely proud and have full confidence in.
The maintenance foundations includes fundamental maintenance principles, it is core methodology. Anyone aiming for success in maintenance must thoroughly understand and adhere to these principles.
This training encapsulates the essence of the maintenance foundations that I've learned, applied, and compared across various companies. To me, it is invaluable, and I wish to share these insights with those fortunate enough to encounter them.
I confirm that this is the most practical and realistic lecture on maintenance foundation across all platforms.
Reflecting on my experience, I have not change many companies. I have spent time to fully experience the maintenance systems of each manufacturing plant. I have worked for an international food and beverage company and later for an electronic equipment manufacturing company. I believe my maintenance foundations are universally applicable and definitely brings substantial and tangible benefits.
To prove my claims, here are some key performance indicators (KPIs) that improved after implementing the maintenance foundations:
1. Machine downtime significantly reduced by over 25% in the first 3 months, followed by a 50% reduction in 6 months. Mean Time Between Failures (MTBF) increased by over 50% from 24.5 hours to 51 hours. Note: These figures may vary depending on the industry and machine conditions.
2. Overall Equipment Efficiency (OEE), a measure of machine performance, increased by at least 7%, reaching approximately 90% after 6 months.
3. Maintenance costs reduced by approximately 10% annually.
Lastly, and importantly for us maintenance engineers, improved peace of mind allows for restful nights and days off.
With my experience and maintenance principles in mind, if existing maintenance foundations are not implemented effectively, advanced maintenance methods such as Total Productive Maintenance (TPM) or Reliability-Centered Maintenance (RCM) should not be applied.
Enroll and increase your maintenance/machine performance now!
Who this course is for:
- All engineers need to improve maintenance/machine performance
- Engineers who implemented TPM/RCM but not successfully
- Fresh maintenance engineers
- Engineering students want to learn about maintenance management
User Reviews
Rating
Eric Dao
Instructor's Courses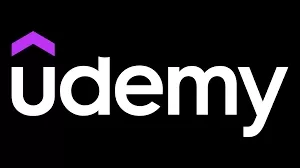
Udemy
View courses Udemy- language english
- Training sessions 11
- duration 2:06:55
- Release Date 2024/11/17