Lean Office for Management Consultants
Asen Gyczew
5:09:39
Description
A practical guide on how to optimize the work in offices using Lean Manufacturing techniques
What You'll Learn?
- Find potential improvements in the Office
- Apply Lean Manufacturing in Offices
- Conduct analyses in Excel of potential savings
- Estimate costs and benefits in Excel
- Find and remove bottlenecks
- Find the optimal location for the office
- Increase the work done by the office
Who is this for?
What You Need to Know?
More details
DescriptionWhat is the aim of this course?
Lean Manufacturing techniques are great tools used to optimize the work in factories and warehouses. The same tools can be used to drastically increase efficiency as well as results in offices. In this course, I will teach you how to use lean manufacturing techniques to optimize the work in the offices.
In the course, you will learn the following things:
What does the office produce?
What kind of waste can you have in the office?
How to apply lean manufacturing techniques in the office to lower costs and increase profits
How to perform analyses related to optimization in Excel
How to remove bottlenecks stopping the firm from growing
This course is based on my 15 years of experience as a consultant in top consulting firms and as a Board Member responsible for strategy, performance improvement, and turn-arounds in the biggest firms from Retail, FMCG, SMG, B2B, and services sectors that I worked for. I have carried out or supervised over 90 different performance improvement projects in different industries that generated a total of 2 billion in additional EBITDA. On the basis of what you will find in this course, I have trained in person over 100 consultants, business analysts, and managers who now are Partners in PE and VC funds, Investment Directors and Business Analysts in PE and VC, Operational Directors, COO, CRO, CEO, Directors in Consulting Companies, Board Members, etc. On top of that my courses on Udemy were already taken by more than 224 000 students including people working in EY, McKinsey, Walmart, Booz Allen Hamilton, Adidas, Naspers, Alvarez & Marsal, PwC, Dell, Walgreens, Orange, and many others.
I teach through case studies, so you will have a lot of lectures showing examples of analyses, and tools that we use. To every lecture, you will find attached (in additional resources) the Excels as well as additional presentations, and materials shown in the lectures so as a part of this course you will also get a library of ready-made analyses that can, with certain modifications, be applied by you or your team in your work.
Why have I decided to create this course?
Optimizing processes in the offices is not that easy. Itâs difficult to see the whole process and define what people should be doing. Most firms, donât give you the full toolbox that you need to optimize processes in the office. This may lead to huge frustration during optimization projects and a lot of inefficiencies.
Therefore, I have decided to create this course that will help students apply lean manufacturing techniques in optimizing processes in the office. The course will give you the knowledge and insight into real-life case studies that will make your life during optimization projects. Thanks to this course, you will know what and how to do during projects aiming at improving the work of the office. You will master how to analyze data and draw conclusions from the analyses. On top of that, you will also master the essential lean manufacturing techniques.
To sum it up, I believe that if you want to become a world-class Management Consultant or Business Analyst you have to have a pretty decent understanding of lean manufacturing techniques and the know-how to apply them in optimizing the work in offices. That is why, I highly recommend this course to Management Consultants or Business Analysts, especially those that are optimizing processes in offices. The course will help you become an expert in lean manufacturing on the level of McKinsey, BCG, Bain, and other top consulting firms.
In what way will you benefit from this course?
The course is a practical, step-by-step guide loaded with tons of analyses, tricks, and hints that will significantly improve the speed with which you understand, and analyze businesses. There is little theory â mainly examples, a lot of tips from my own experience as well as other notable examples worth mentioning. Our intention is that thanks to the course you will learn:
What does the office produce?
What kind of waste can you have in the office?
How to apply lean manufacturing techniques in the office to lower costs and increase profits
How to perform analyses related to optimization in Excel
How to remove bottlenecks stopping the firm from growing
You can also ask me any question either through the discussion field or by messaging me directly.
How the course is organized?
The course is divided currently into the following sections:
Introduction. We begin with a little introduction to the course as well as some general info on how the course is organized.
What does the office produce? Most offices are actually very similar to factories. They produce certain goods and services and have almost the same problems as every factory. In this section, we will look at similarities and differences.
Basic Lean Methods. In this section, we will have a look at the essential lean manufacturing techniques that will help you significantly increase productivity at your office.
Personal Productivity. A lot can be achieved by increasing Personal Productivity. In this section, we will briefly have a look at what methods are the most useful. In Additional Resources, there will be an additional longer presentation on that.
Remove Bottlenecks. In the Office, you will have plenty of bottlenecks that are preventing the firm from growing faster. In this section, we will see how you remove bottlenecks in practice.
Kanban. Another great concept from Lean Manufacturing that is widely used in the office is the so-called Kanban. In this section, we will see how it can be used for improving office work.
Continuous Flow. In this section, we will discuss what a continuous flow is and how you can create it.
Other Intermediate Lean Methods. In this section, we will look at other lean methods that can prove very useful in your quest to improve the work at the office. We will discuss 5S, Poka Yoke, Milk run, Zero defect rule, and many more.
Increase Throughput. As we have said offices, similar to factories, produce goods and services. In this section, we will see how you can measure that and increase it.
Automation. If you want to be competitive you have to automate the work in the office. This means using more machines and software to support the work of the people. In this section, we will look at how you can analyze the value of automation for the firm.
You will be able also to download many additional resources
1. Useful frameworks and techniques
2. Analyses presented in the course
3. Additional resources
4. Links to additional presentations, articles, and movies
5. Links to books worth reading
At the end of my course, students will be able toâ¦
Find potential improvements in the office
Apply Lean Manufacturing in Offices
Conduct analyses in Excel of potential savings
Estimate costs and benefits in Excel
Find and remove bottlenecks
Find the optimal location for the office
Increase the work done by the office
Who should take this course? Who should not?
Management Consultants
Business Analysts
Managers
Financial Controllers
Directors
Project Managers
What will students need to know or do before starting this course?
Basic or intermediate Excel
Basic knowledge of economics
Basic or intermediate knowledge of finance & accounting
Who this course is for:
- Management Consultants
- Business Analysts
- Managers
- Financial Controllers
- Project Managers
- HR Directors
What is the aim of this course?
Lean Manufacturing techniques are great tools used to optimize the work in factories and warehouses. The same tools can be used to drastically increase efficiency as well as results in offices. In this course, I will teach you how to use lean manufacturing techniques to optimize the work in the offices.
In the course, you will learn the following things:
What does the office produce?
What kind of waste can you have in the office?
How to apply lean manufacturing techniques in the office to lower costs and increase profits
How to perform analyses related to optimization in Excel
How to remove bottlenecks stopping the firm from growing
This course is based on my 15 years of experience as a consultant in top consulting firms and as a Board Member responsible for strategy, performance improvement, and turn-arounds in the biggest firms from Retail, FMCG, SMG, B2B, and services sectors that I worked for. I have carried out or supervised over 90 different performance improvement projects in different industries that generated a total of 2 billion in additional EBITDA. On the basis of what you will find in this course, I have trained in person over 100 consultants, business analysts, and managers who now are Partners in PE and VC funds, Investment Directors and Business Analysts in PE and VC, Operational Directors, COO, CRO, CEO, Directors in Consulting Companies, Board Members, etc. On top of that my courses on Udemy were already taken by more than 224 000 students including people working in EY, McKinsey, Walmart, Booz Allen Hamilton, Adidas, Naspers, Alvarez & Marsal, PwC, Dell, Walgreens, Orange, and many others.
I teach through case studies, so you will have a lot of lectures showing examples of analyses, and tools that we use. To every lecture, you will find attached (in additional resources) the Excels as well as additional presentations, and materials shown in the lectures so as a part of this course you will also get a library of ready-made analyses that can, with certain modifications, be applied by you or your team in your work.
Why have I decided to create this course?
Optimizing processes in the offices is not that easy. Itâs difficult to see the whole process and define what people should be doing. Most firms, donât give you the full toolbox that you need to optimize processes in the office. This may lead to huge frustration during optimization projects and a lot of inefficiencies.
Therefore, I have decided to create this course that will help students apply lean manufacturing techniques in optimizing processes in the office. The course will give you the knowledge and insight into real-life case studies that will make your life during optimization projects. Thanks to this course, you will know what and how to do during projects aiming at improving the work of the office. You will master how to analyze data and draw conclusions from the analyses. On top of that, you will also master the essential lean manufacturing techniques.
To sum it up, I believe that if you want to become a world-class Management Consultant or Business Analyst you have to have a pretty decent understanding of lean manufacturing techniques and the know-how to apply them in optimizing the work in offices. That is why, I highly recommend this course to Management Consultants or Business Analysts, especially those that are optimizing processes in offices. The course will help you become an expert in lean manufacturing on the level of McKinsey, BCG, Bain, and other top consulting firms.
In what way will you benefit from this course?
The course is a practical, step-by-step guide loaded with tons of analyses, tricks, and hints that will significantly improve the speed with which you understand, and analyze businesses. There is little theory â mainly examples, a lot of tips from my own experience as well as other notable examples worth mentioning. Our intention is that thanks to the course you will learn:
What does the office produce?
What kind of waste can you have in the office?
How to apply lean manufacturing techniques in the office to lower costs and increase profits
How to perform analyses related to optimization in Excel
How to remove bottlenecks stopping the firm from growing
You can also ask me any question either through the discussion field or by messaging me directly.
How the course is organized?
The course is divided currently into the following sections:
Introduction. We begin with a little introduction to the course as well as some general info on how the course is organized.
What does the office produce? Most offices are actually very similar to factories. They produce certain goods and services and have almost the same problems as every factory. In this section, we will look at similarities and differences.
Basic Lean Methods. In this section, we will have a look at the essential lean manufacturing techniques that will help you significantly increase productivity at your office.
Personal Productivity. A lot can be achieved by increasing Personal Productivity. In this section, we will briefly have a look at what methods are the most useful. In Additional Resources, there will be an additional longer presentation on that.
Remove Bottlenecks. In the Office, you will have plenty of bottlenecks that are preventing the firm from growing faster. In this section, we will see how you remove bottlenecks in practice.
Kanban. Another great concept from Lean Manufacturing that is widely used in the office is the so-called Kanban. In this section, we will see how it can be used for improving office work.
Continuous Flow. In this section, we will discuss what a continuous flow is and how you can create it.
Other Intermediate Lean Methods. In this section, we will look at other lean methods that can prove very useful in your quest to improve the work at the office. We will discuss 5S, Poka Yoke, Milk run, Zero defect rule, and many more.
Increase Throughput. As we have said offices, similar to factories, produce goods and services. In this section, we will see how you can measure that and increase it.
Automation. If you want to be competitive you have to automate the work in the office. This means using more machines and software to support the work of the people. In this section, we will look at how you can analyze the value of automation for the firm.
You will be able also to download many additional resources
1. Useful frameworks and techniques
2. Analyses presented in the course
3. Additional resources
4. Links to additional presentations, articles, and movies
5. Links to books worth reading
At the end of my course, students will be able toâ¦
Find potential improvements in the office
Apply Lean Manufacturing in Offices
Conduct analyses in Excel of potential savings
Estimate costs and benefits in Excel
Find and remove bottlenecks
Find the optimal location for the office
Increase the work done by the office
Who should take this course? Who should not?
Management Consultants
Business Analysts
Managers
Financial Controllers
Directors
Project Managers
What will students need to know or do before starting this course?
Basic or intermediate Excel
Basic knowledge of economics
Basic or intermediate knowledge of finance & accounting
Who this course is for:
- Management Consultants
- Business Analysts
- Managers
- Financial Controllers
- Project Managers
- HR Directors
User Reviews
Rating
Asen Gyczew
Instructor's Courses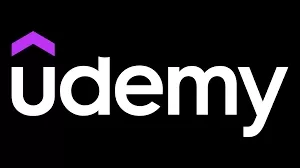
Udemy
View courses Udemy- language english
- Training sessions 109
- duration 5:09:39
- English subtitles has
- Release Date 2024/04/13