Lean for Business Organizations
Sorin Dumitrascu
8:35:37
Description
Applying Lean in Service and Manufacturing Organizations
What You'll Learn?
- Introduction to Lean for Service and Manufacturing
- Using Lean for Perfection and Quality
- Lean Tools and Techniques for Flow and Pull
- Reducing Waste and Streamlining Value Flow Using Lean
- Value Stream Mapping in Lean Business
- Applying Lean in Service and Manufacturing Organizations
Who is this for?
What You Need to Know?
More details
DescriptionThe Lean for Business Organizations course includes the following 6 sections:
Introduction to Lean for Service and Manufacturing,
Using Lean for Perfection and Quality,
Lean Tools and Techniques for Flow and Pull,
Reducing Waste and Streamlining Value Flow Using Lean,
Value Stream Mapping in Lean Business, and
Applying Lean in Service and Manufacturing Organizations.
1. Introduction to Lean for Service and Manufacturing
Using inefficient procedures is like digging a 200-foot wide hole for a 100-foot wide house. You'll have wasted a great deal of effort on something you don't really need. Your organization must make shrewd investments in its precious time, money, and effort. You need flexible, intelligent strategies to evolve and prosper in a competitive global market.
Lean is a methodology that incorporates a powerful set of tools and techniques designed to maximize customer value while constantly working to reduce waste. It focuses on improving overall efficiency, quality, and customer satisfaction.
Because of its ability to improve customer satisfaction and deliver bottom-line financial gains, Lean is a preferred strategic choice for many organizations.
This course introduces you to the basic principles of Lean, which will help you create more efficient processes and get you on the road to successful operations management.
This course also outlines the five-step process for implementing Lean. By learning how to implement Lean in your organization, you can reduce the costs of developing your company's product, increase production efficiency, and improve safety, quality, and performance levels.
Finally, the course explains how Lean integrates with the Six Sigma production management system. Using this hybrid approach enables you to minimize process and product defects, and to identify and resolve pervasive problems.
2. Using Lean for Perfection and Quality
Today's markets are very competitive and customers insist on the best quality products for their money. This means that businesses must actively pursue perfection to keep their customers and to retain their market share.
Pursuing perfection and excellent quality are important principles of Lean thinking.
Continuous improvement, the elimination of waste, and striving toward zero defects all help organizations attract and keep customers, and so increase their profitability.
This course introduces four Lean tools organizations use to strive for perfection and improve quality â 5S, Hoshin Kanri, jidoka and poka yoke, and standard work.
As you work through this course, you'll find out what these tools are, their purpose, and how the tools are used.
You should then be able to recognize how the tools may be used in your own organization.
The course provides examples of how the Lean tools can be applied in both manufacturing and service organizations. It will help you assess your own organization's needs and determine how you can apply the tools to perfect what you offer.
3. Lean Tools and Techniques for Flow and Pull
How can you make your organization more efficient? The simplest way is to eliminate waste from your processes. This waste can be caused by many factors, such as untidy workspaces and surplus inventory. Or it might be caused by inefficient distribution of work. Using Lean tools, you can make your processes smoother and your workspaces tidier.
To implement a Lean solution, you must know what tools and techniques are available, and which ones would best help you. You have to select the best blend of Lean techniques for your organization. You can use a number of Lean techniques to make your organization run more smoothly. These include the visual workplace, just-in-time, kanban, and line balancing.
The visual workplace uses signs and other visual cues to convey information quickly. The visual cues include work instructions, process flow diagrams, and status boards.
Just-in-time ensures that you have exactly the right amount of supplies needed at any time. This helps to reduce surplus inventory.
Kanban cards are triggers that alert the team to send more parts or supplies. The parts are then "pulled" into the system, based on demand.
Line balancing results in the even distribution of work among workers. No workers are overburdened, and no workers are left idle.
Using the Lean techniques outlined in this course will help you to develop strategies for improving flow and pull in your organization.
4. Reducing Waste and Streamlining Value Flow Using Lean
For your business to be the best it can be, you need to eliminate what doesn't work and improve what does. In Lean thinking, this translates to reducing or eliminating waste and improving the flow of production. This course introduces approaches you can use to do just that, in both the manufacturing and service environments.
Before you can reduce waste, you need to recognize where and how it's occurring.
In this course, you'll learn how to do this by determining which of your company's activities add value and which don't.
Once you've categorized activities, you can search for ways to eliminate those that don't add value or, if they're required, to minimize the resources spent on them. And for activities that do add value, you can find ways to optimize this value.
Next you'll learn about the different forms of waste that you find in a business and the typical causes of each type of waste.
You'll also learn various strategies for minimizing or eliminating each of the waste types.
This course also explains the concept of continuous flow, which depends on the removal of obstacles and bottlenecks in work processes. You'll learn how to balance work processes to enhance flow, with the aim of producing what's needed, when it's needed, in the quantities required.
Using the strategies outlined in this course can improve the efficiency of your business, moving its processes closer to perfection.
5. Value Stream Mapping in Lean Business
Suppose on your first day of work, your boss tells you too many defects have crept into the company's product. She then asks for your input on how to solve the problem. But without knowing how the company's current processes work, it's unlikely you'll have useful suggestions. To improve processes, you first need to understand them.
To understand how something works, you need to observe it, noting how it fits into a larger pattern.
Creating a visual representation of the material and information flow that leads to the creation of a product or service can help. This is called value stream mapping.
With a value stream map, you can search for flaws, work out why problems exist, and plan how to eliminate them.
This course teaches you how to use value stream mapping as a tool for improving an organization's processes and making them more efficient. You'll learn how to create a current-state value stream map, analyze the current state, and then create a future-state map.
Create a current-state map - The course provides an overview of the steps involved in creating a current-state map and of the symbols typically used in this type of map.
Analyze current state - The current-state map provides a big-picture view of a targeted process. This makes it easier to identify where waste is occurring and why.
Create a future-state map - You'll learn how to create a future-state value stream map. This involves searching for and then recording opportunities to balance the production line, create pull, and eliminate sources of waste.
In this course, you'll learn how value stream mapping can be used, in both manufacturing and service industries. It will prove a valuable tool you can use to improve efficiency and eliminate waste, ultimately boosting both customer satisfaction and an organization's profits.
6. Applying Lean in Service and Manufacturing Organizations
Despite the relative simplicity of many Lean tools, a majority of attempts to adopt Lean in an organization fail. Why does this happen?
The chief cause of failure to convert to a Lean enterprise is lack of awareness that it requires a culture change, rather than simply a change in tools.
Transformation to a Lean enterprise calls for a complete change in the way everyone in the organization thinks about work, as well as slight work modifications.
Flirting with Lean tools won't create a meaningful or lasting improvement in an organization. To truly embrace and integrate Lean principles, an organization has to make a long-term commitment to the change. It also has to change its culture. All employees need to practice applying Lean concepts daily, until Lean thinking becomes an accepted and routine part of how they think and behave. It requires a cultural change.
A permanent shift to the Lean philosophy can occur only from a continuous improvement philosophy. When this occurs, organizational and customer benefits will be realized. So you need to encourage and practice continuous improvement daily to truly integrate the shift in culture.
This course provides a guide to the benefits and characteristics of a Lean culture. It provides tips and strategies for facilitating a culture change through the use of kaizen. And it provides a detailed guide on how to plan for and implement a kaizen event in your organization.
Thatâs it! Now go ahead and push that âTake this courseâ button and see you on the inside!
Who this course is for:
- Individuals who have responsibility for reducing costs and waste, and improving efficiency and customer value at the organizational level
The Lean for Business Organizations course includes the following 6 sections:
Introduction to Lean for Service and Manufacturing,
Using Lean for Perfection and Quality,
Lean Tools and Techniques for Flow and Pull,
Reducing Waste and Streamlining Value Flow Using Lean,
Value Stream Mapping in Lean Business, and
Applying Lean in Service and Manufacturing Organizations.
1. Introduction to Lean for Service and Manufacturing
Using inefficient procedures is like digging a 200-foot wide hole for a 100-foot wide house. You'll have wasted a great deal of effort on something you don't really need. Your organization must make shrewd investments in its precious time, money, and effort. You need flexible, intelligent strategies to evolve and prosper in a competitive global market.
Lean is a methodology that incorporates a powerful set of tools and techniques designed to maximize customer value while constantly working to reduce waste. It focuses on improving overall efficiency, quality, and customer satisfaction.
Because of its ability to improve customer satisfaction and deliver bottom-line financial gains, Lean is a preferred strategic choice for many organizations.
This course introduces you to the basic principles of Lean, which will help you create more efficient processes and get you on the road to successful operations management.
This course also outlines the five-step process for implementing Lean. By learning how to implement Lean in your organization, you can reduce the costs of developing your company's product, increase production efficiency, and improve safety, quality, and performance levels.
Finally, the course explains how Lean integrates with the Six Sigma production management system. Using this hybrid approach enables you to minimize process and product defects, and to identify and resolve pervasive problems.
2. Using Lean for Perfection and Quality
Today's markets are very competitive and customers insist on the best quality products for their money. This means that businesses must actively pursue perfection to keep their customers and to retain their market share.
Pursuing perfection and excellent quality are important principles of Lean thinking.
Continuous improvement, the elimination of waste, and striving toward zero defects all help organizations attract and keep customers, and so increase their profitability.
This course introduces four Lean tools organizations use to strive for perfection and improve quality â 5S, Hoshin Kanri, jidoka and poka yoke, and standard work.
As you work through this course, you'll find out what these tools are, their purpose, and how the tools are used.
You should then be able to recognize how the tools may be used in your own organization.
The course provides examples of how the Lean tools can be applied in both manufacturing and service organizations. It will help you assess your own organization's needs and determine how you can apply the tools to perfect what you offer.
3. Lean Tools and Techniques for Flow and Pull
How can you make your organization more efficient? The simplest way is to eliminate waste from your processes. This waste can be caused by many factors, such as untidy workspaces and surplus inventory. Or it might be caused by inefficient distribution of work. Using Lean tools, you can make your processes smoother and your workspaces tidier.
To implement a Lean solution, you must know what tools and techniques are available, and which ones would best help you. You have to select the best blend of Lean techniques for your organization. You can use a number of Lean techniques to make your organization run more smoothly. These include the visual workplace, just-in-time, kanban, and line balancing.
The visual workplace uses signs and other visual cues to convey information quickly. The visual cues include work instructions, process flow diagrams, and status boards.
Just-in-time ensures that you have exactly the right amount of supplies needed at any time. This helps to reduce surplus inventory.
Kanban cards are triggers that alert the team to send more parts or supplies. The parts are then "pulled" into the system, based on demand.
Line balancing results in the even distribution of work among workers. No workers are overburdened, and no workers are left idle.
Using the Lean techniques outlined in this course will help you to develop strategies for improving flow and pull in your organization.
4. Reducing Waste and Streamlining Value Flow Using Lean
For your business to be the best it can be, you need to eliminate what doesn't work and improve what does. In Lean thinking, this translates to reducing or eliminating waste and improving the flow of production. This course introduces approaches you can use to do just that, in both the manufacturing and service environments.
Before you can reduce waste, you need to recognize where and how it's occurring.
In this course, you'll learn how to do this by determining which of your company's activities add value and which don't.
Once you've categorized activities, you can search for ways to eliminate those that don't add value or, if they're required, to minimize the resources spent on them. And for activities that do add value, you can find ways to optimize this value.
Next you'll learn about the different forms of waste that you find in a business and the typical causes of each type of waste.
You'll also learn various strategies for minimizing or eliminating each of the waste types.
This course also explains the concept of continuous flow, which depends on the removal of obstacles and bottlenecks in work processes. You'll learn how to balance work processes to enhance flow, with the aim of producing what's needed, when it's needed, in the quantities required.
Using the strategies outlined in this course can improve the efficiency of your business, moving its processes closer to perfection.
5. Value Stream Mapping in Lean Business
Suppose on your first day of work, your boss tells you too many defects have crept into the company's product. She then asks for your input on how to solve the problem. But without knowing how the company's current processes work, it's unlikely you'll have useful suggestions. To improve processes, you first need to understand them.
To understand how something works, you need to observe it, noting how it fits into a larger pattern.
Creating a visual representation of the material and information flow that leads to the creation of a product or service can help. This is called value stream mapping.
With a value stream map, you can search for flaws, work out why problems exist, and plan how to eliminate them.
This course teaches you how to use value stream mapping as a tool for improving an organization's processes and making them more efficient. You'll learn how to create a current-state value stream map, analyze the current state, and then create a future-state map.
Create a current-state map - The course provides an overview of the steps involved in creating a current-state map and of the symbols typically used in this type of map.
Analyze current state - The current-state map provides a big-picture view of a targeted process. This makes it easier to identify where waste is occurring and why.
Create a future-state map - You'll learn how to create a future-state value stream map. This involves searching for and then recording opportunities to balance the production line, create pull, and eliminate sources of waste.
In this course, you'll learn how value stream mapping can be used, in both manufacturing and service industries. It will prove a valuable tool you can use to improve efficiency and eliminate waste, ultimately boosting both customer satisfaction and an organization's profits.
6. Applying Lean in Service and Manufacturing Organizations
Despite the relative simplicity of many Lean tools, a majority of attempts to adopt Lean in an organization fail. Why does this happen?
The chief cause of failure to convert to a Lean enterprise is lack of awareness that it requires a culture change, rather than simply a change in tools.
Transformation to a Lean enterprise calls for a complete change in the way everyone in the organization thinks about work, as well as slight work modifications.
Flirting with Lean tools won't create a meaningful or lasting improvement in an organization. To truly embrace and integrate Lean principles, an organization has to make a long-term commitment to the change. It also has to change its culture. All employees need to practice applying Lean concepts daily, until Lean thinking becomes an accepted and routine part of how they think and behave. It requires a cultural change.
A permanent shift to the Lean philosophy can occur only from a continuous improvement philosophy. When this occurs, organizational and customer benefits will be realized. So you need to encourage and practice continuous improvement daily to truly integrate the shift in culture.
This course provides a guide to the benefits and characteristics of a Lean culture. It provides tips and strategies for facilitating a culture change through the use of kaizen. And it provides a detailed guide on how to plan for and implement a kaizen event in your organization.
Thatâs it! Now go ahead and push that âTake this courseâ button and see you on the inside!
Who this course is for:
- Individuals who have responsibility for reducing costs and waste, and improving efficiency and customer value at the organizational level
User Reviews
Rating
Sorin Dumitrascu
Instructor's Courses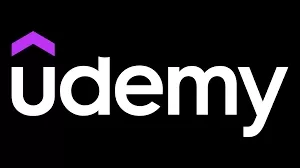
Udemy
View courses Udemy- language english
- Training sessions 95
- duration 8:35:37
- Release Date 2024/02/05